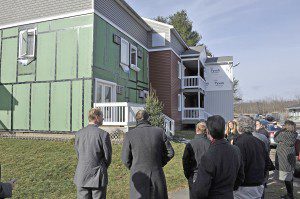
Officials from the U.S. Department of Housing and Urban Development along with Peabody Properties and contractors tour the Powdermill Village in Westfield, where $3 million of energy conservation upgrades were put into place. (Photo by Frederick Gore)
WESTFIELD – A $2 billion federal initiative from the Department of Housing and Urban Development (HUD) known as the Better Buildings Challenge has been expanded to improve the energy efficiency of multifamily housing units and developments throughout the United States.
In the Commonwealth of Massachusetts, 12 affordable housing communities will be receiving energy efficient makeovers thanks to the Better Buildings Challenge, with Westfield’s Powdermill Village, an affordable housing community located on 126 Union Street, among them.
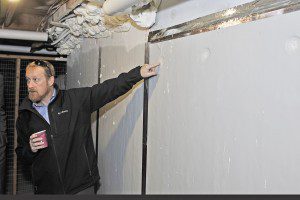
Tom Hartman, of Coldham & Hartman Architects, points out the new R-12 wall insulation panels mounted on the exterior walls of the basements of the Powdermill Village in Westfield where a $3 million energy conservation program was recently completed. (Photo by Frederick Gore)
The housing community is currently undergoing $3 million worth of upgrades, $2.3 million of which went toward mechanical and electrical systems, and $425,000 that went into improving the exterior of one of the community’s 12 buildings.
Thursday morning, a coalition made up of representatives from HUD, MassHousing, Boston Community Capital, Coldham & Hartman Architects of Amherst and Peabody Properties, Inc., the Braintree-based real estate firm which owns Powdermill Village, took a tour of one of the facilities to highlight the improvements.
“We’ve done something that is relatively transformative for an affordable community which is in the world that we all work in, enjoy and support,” said Michael Ferguson of Peabody Properties, Inc., adding that the energy savings will help to cover the low repayments of the project.
“If money is the barrier (for future projects), we can overcome that barrier with energy savings,” he said.
Powdermill Village, which has built in 1972, consists of 12 buildings divided into 250 housing units, with each unit containing 18 to 22 sub-units each which range in size from 835 square foot, one-bedroom apartments to 1,540 square foot, three bedroom units.
The oil boilers being replaced were installed in 2000, when the community was last renovated with new siding, roofs, windows and in-unit finishes.
The $2.3 million spent on improvements to the mechanical and electrical systems included the replacement of boilers, adding indirect tanks and a loop for domestic hot water, the removal of in-unit electric water heaters, conversion of exterior and basement lights to LED/CFL in all buildings and the replacement of toilets, aerators and showerheads in all units.
The $425,000 exterior improvements to one of the buildings was spent replacing rotten pieces of the exterior and adding two inches of insulation, installing triple-glazed windows, replacing sliding glass doors with patio doors, insulating basements and crawl spaces, and upgrading the building’s unit ventilation.
Ferguson stated that the oversized, aging oil-fired boilers had grown “relatively inefficient” and that the new boilers were far superior.
“They’re small, wall-mounted spaceships that do fantastic things. They have an automatic transmission, so to speak, where – if it is low demand – it operates low,” said Ferguson. “We’ve taken advantages of oil prices in recent weeks. It still outweighs the cost of gas.”
Ferguson said that the projects will be completed by December 18.
“We’re using state-of-the-art technology such as a true remote control where, through a web-based interface, we can log on, look at the boilers and change their settings without having to drive out here,” he said.
Dan Mahr, president of Aalanco Service Corp., the Westborough-based HVAC service company who handled the installation of the boilers, said the new systems had an efficiency of 95 percent, in stark contrast to the 70 percent efficiency of the old boilers.
“These are probably the most modern boiler setups on the market right now,” he said of the fourth-generation condensing boiler installed in the building where the exterior improvements were taking place. “I’m hoping these boilers can last 20 to 30 years.”
Mahr said that two boilers were installed in the community, in addition to the 12 placed in each building and said that the heating side of the project cost $1 million, while the domestic hot water systems cost around $700,000.
Asked how long it would take these boilers to become obsolete, Mahr said he couldn’t say.
“The rate of change for condensing boilers… I saw the first one 10-15 years ago and they’ve just continuously progressed,” he said. “When they first came out, they were hardly any water, hardly metal. Now, they have a lot more of each and are still a lot more structurally sound.”
